Above: The PSM Puma IFV has hydro-pneumatic suspension for a high level of cross-country mobility. (Photo: PSM)
Foss Unglossed: Balancing the scales - keeping AFVs mobile in an era of weight gain
The three cornerstones of armoured fighting vehicles (AFVs), tracked and wheeled, are protection, tactical mobility and firepower, with each of these having many sub-elements, but this is about to change (or at least it should!)
This special IDEF 2025 Shephard Views Newsletter is presented in partnership with Otokar
In my view, strategic mobility should be added, as an increasing number of AFVs have rapidly increased in mass as the end user requests more volume, payload and armour. All useful stuff, but they push up gross vehicle weights (GVWs) by a significant amount. This means they are unlikely be able to move to forward deployment without support, be it road or rail. Flying them in is usually not an option due to cost and non-availability of suitable aircraft.
The weight gain also means that tank transporters (or rather heavy equipment transporters (HETs) as I should now call them), as well as military bridging must be upgraded or replaced to account for these ballooning GVWs.
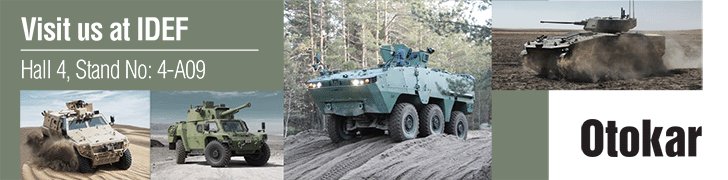
Explore armored vehicles and turret systems of Otokar, the global land systems manufacturer.
Many 8x8 AFVs are now over 30 tonnes with the ARTEC Boxer already coming in at more than 40. If we then accept strategic mobility as a fourth “pillar”, how do you balance it against the other three (and those with each other) as platform size balloons?
A bigger gun surrounded by lots of armour usually means a more dangerous enemy. For many years during the USSR rated the British Chieftain tank as the greatest threat due not only to its armour levels but its 120mm rifled gun. The contemporary Leopard 1, AMX-30 and M60 all had a 105mm gun and less protection. But the Chieftain was by far the heaviest and slowest.
One wonders how the Russians rank all the various Western MBTs they encounter (and even capture) in Ukraine. I suspect we won’t know for a decade or two…
Above: A Hanwha K21 IFV is put through its paces in mobility tests ,including fording. (Photo: Hanwha Aerospace)
Tactical mobility meanwhile encompasses several elements including the power pack. Today nearly all MBTs have a diesel engine coupled to an automatic or semi-automatic transmission (the US M1 Abrams and Russia’s T-80U are the gas turbine exceptions). Diesels are favoured due to their fuel efficiency and lower cost.
Hybrid-electric drives have been tested on many AFVs, mainly wheeled, but none has entered mass production so far, although this could rapidly change. But it seems the early drive by military forces for decarbonisation at the start of the decade has lost its impetus in the light of increasing threats and the need for rapid rearmament. Artillery bombardments and drone strikes on your cities are not especially good for the environment either!
An auxiliary power unit (APU) is useful (and has been standard on all British MBTs since the Centurion). The APU allows all key subsystems to be run with the main engine switched off to save power.
Originally introduced to increase the main engine’s life (by not using it as much), the APU is increasingly needed to drive the ever-growing range of equipment on board that needs electrical power, such as battle management systems, remote weapon stations, air conditioning and defensive aids suites.
Then of course there is the tracks vs wheels question. I’ll keep the discussion brief this time (some regular readers may breathe a sigh of relief!) In simple terms if you want to move heavy loads over mud, you need tracks. If you don’t, wheels are less costly and more reliable.
Tracked AFVs have much lower ground pressure as the tracks have more contact with the surface. They are normally lower in profile there are no large wheels to take up space and add height. The first advantage disappears if you don’t have a lot of weight to carry.
Wheeled vehicles have lower life cycle costs and can rapidly be deployed over long distances without needing an HET. Runflats also mean that a “puncture” no longer immobilises your AFV.
A central tyre inflation system is also offered as an option on most wheeled AFVs and an increasing number of high-mobility trucks. The system is operated by the driver remotely and allows them to adjust tyre pressure according to the terrain. When going over soft sand, for example, air is let out to increase the area of the tyre in contact with the ground.
Traditionally tracks were all steel, with some using rubber pads to avoid damaging road surfaces and reducing noise (a little – I don’t think we’ll ever see a silent tank!) Composite rubber tracks (CRT) have been developed, most notably by Canada’s Soucy International, and these have been fitted to tracked IFVs such as the BAE Systems CV90 and Hanwha Redback.
A CRT’s advantages include lower noise levels, less vibration and weight saving, as well as reduced rolling resistance which translates to an increase in operational range.
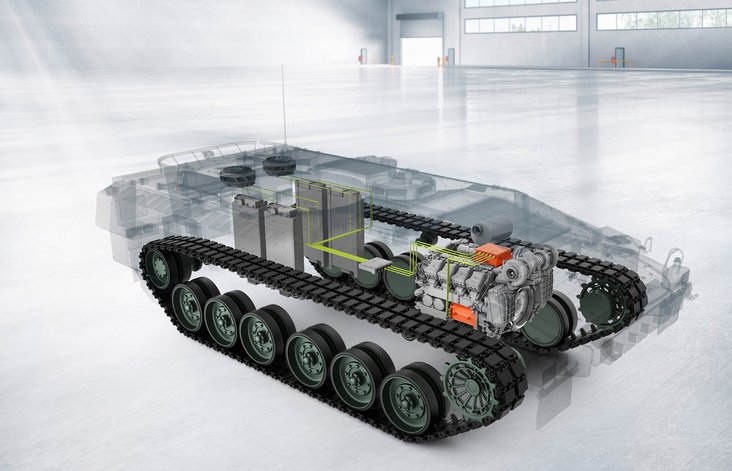
Above: Rolls Royce Power Systems is one of several companies currently studying hybrid-electric drive solutions for tracked vehicles. (Image: Rolls Royce Power Systems)
Perhaps surprisingly, the maximum speed of tracked AFVs has not changed over the last century and for many years the record was held by a US M1931 with Walter Christie suspension (T-34 style) well before World War II. The official international speed record for a tracked military vehicle is 82.23km/h, held by an ex-British Army Scorpion modified by Repaircraft in 2002.
This record is at risk from Howe & Howe’s Ripsaw F4 which is claimed to be able to achieve over 100km/h. Either way, these speeds seem relatively slow compared to wheeled vehicles.
And then there’s the human factor. In many respects the mobility of an AFV over rough terrain is limited by what the crew can take.
Vehicles with a high degree of wheel travel and good ground clearance can absorb rough terrain at speed (think M1 Abrams, Patria AMV and Challenger), whereas designs with limited wheel travel (M60, Centurion, Land Rover Defender) struggle with crew comfort.
Tracked vehicles made use of torsion-bar suspension for many years due to its simplicity and effectiveness, but there is now a preference for hydro-pneumatic systems. These save space in the lower part of the hull, give an improved ride for the crew and make for a more stable firing platform.
It is not all good news - hydro-pneumatics are more expensive, less reliable and affected by changes in temperature increasing their stiffness. Nonetheless, all versions of the UK Challenger MBT as well as Germany’s Puma IFV make use of them.
Some MBTs, such as South Korea’s K1 and K2 have a hydro-pneumatic system that allows the driver to raise or lower the height of the vehicle or tilt it forward or rearward. The consequent ability to increase depression of the main armament can be useful in many tactical situations, especially engaging targets when the MBT is firing from a reverse slope.
In future some AFVs may adopt active suspension (the Swedish CV9040 has a form of it already) which allows the platform to adjust ride to terrain without driver assistance. However, cost constraints will likely limit its deployment, especially on heavier vehicles.
But no matter how high-tech your suspension is, both tracked and wheeled AFVs passing over the same area of ground, such as beachheads, river crossings and choke points, can make the terrain almost impassable. Mud and sand will always be a feature of land warfare!
Returning to the triangle of mobility, firepower and protection, the current war in Ukraine has shown how armoured low-cost drones can effectively destroy even the most expensive and best-protected vehicles on the battlefield. Time to rethink the balance?
The trend towards robotic vehicles, either in support or in place of crewed platforms, is also changing the equation. If you can limit protection and remove the crew, then you can in theory reduce development time. Deploying direct-energy weapons rather than kinetics could offer similar benefits as that technology evolves.
This leads to a future class of AFVs that will be small, wheeled, robotic and expendable. But armies and their vehicle fleets are not going to change overnight. Institutional inertia and the age-old problem of insufficient budgets will see to that.
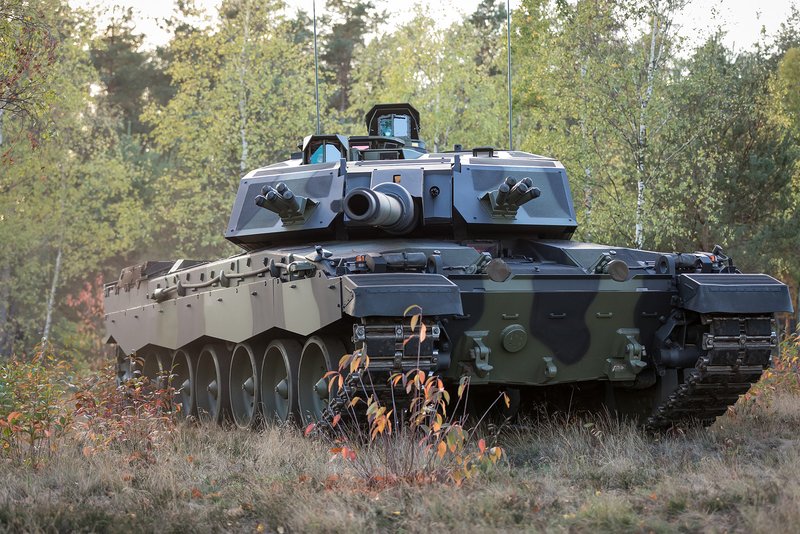
Above: RBSL's Challenger 3 demonstrator clearly showing the commander's and gunner's'sights. Note the driver only has one periscope. (Photo: RBSL))
So crewed AFVs will be with us for a long time yet. And those crews need to know what is going on around them. A typical MBT has a complement of three or four (driver, commander, gunner and sometimes still a loader), all of whom require optical devices for situational awareness and engaging the target.
In the past the driver normally had a single day periscope, but this only gave a limited field of view, so the trend is to have at least three, normally located in the forward part of the hatch cover. The gunner normally has just one day periscope, although some are mounted so that they can traverse through 360 degrees.
The commander meanwhile normally has a cupola with day periscopes to provide all-round cover. On the CV90 this cupola can be slightly raised umbrella-fashion for a quick circular panoramic scan. Commander and gunner also need sighting devices to search for targets.
A commander’s panoramic day/night sight provides rapid situational awareness through 360 degrees and allows hunter/killer engagements to take place. Here the commander acquires the target and then hands over to the gunner to carry out the actual engagement.
Day observation devices were initially supplemented by infrared systems followed by image intensifiers, which are still used on some vehicles. The trend now is towards thermal observation as this allows the crew to see targets through bush and other terrain features under almost all weather conditions.
Modern MBTs and IFVs normally have day/colour cameras attached to the hull to provide situational awareness through a full 360 degrees with images displayed at all crew stations on flat panels which also supply other key information. The driver will have access to rear-view cameras as there have been incidents of vehicles reversing rapidly and running over dismounts.
In addition, IFVs often feature a display in the rear troop compartment which can be viewed by the dismounts. It’s always good to know what you’re (literally) going to be walking into.
While these offer much better viewing than a simple slit or port in the armour, they all add weight, require power and are more vulnerable to damage than direct optics, taking us right back to our original series of trade-offs…
Put simply, you can’t have everything. The best AFV designers will balance the different sides of the triangle (or is it now a rectangle?) to achieve the best outcome for the intended mission set. Performance predictions based on data modelling (and past experience) and computer-aided design should mean the engineers and developers get it right more often than not, but until your AFV is used in a real combat situation you’ll never know for sure. And even a design that’s perfectly tailored to the task will never be immune from outdated tactics, poor command decisions or unforeseen threats.
Note: The author would like to thank Paul Briggs, not only for his input to this piece but also for many years of discussion on various aspects of AFV design, especially mobility and power packs.