Who wants to build ships? Why US yards face a workforce crisis
The USN’s Constellation-class frigates will be delivered at least one year behind schedule. This development, reportedly due to a shortage of welders at the Fincantieri Marinette Marine (FMM) shipyard, was big news in early January. Yet skilled workforce shortages in this sector have been an ongoing issue for years. The important question is why.
Earlier in January, multiple defence media reported that the delivery of the first Constellation-class frigate to the USN would take place at least one year behind schedule. Apparently, the significant – and growing – delay is a result of skilled workforce shortages, in particular welders, at FMM... Continues below
Newsletter Sponsor:
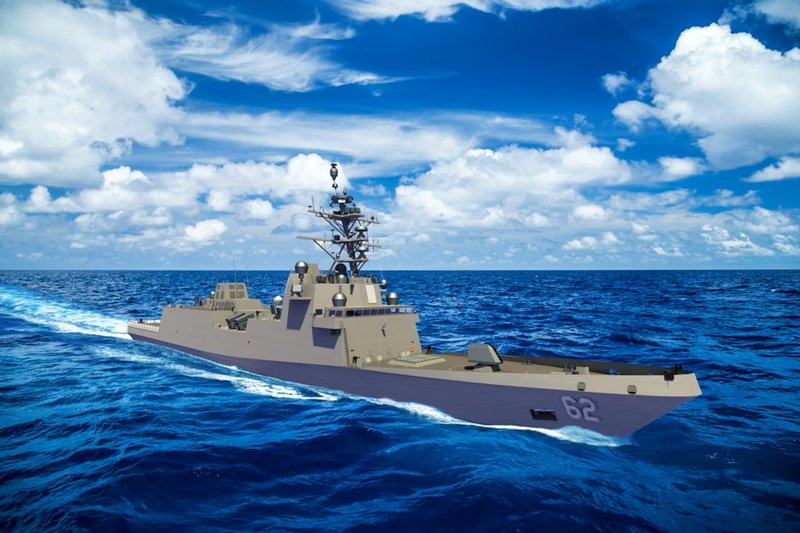
Above: The USN’s first Constellation-class frigate will become a reality at least a year later than planned, reportedly due to a shortage of skilled welders. (Image: USN)
Why this is considered news is a little baffling, as alarm bells have been ringing constantly in the industry over the past few years. What should be the real story is why nothing has been done about it yet.
This issue was raised back in 2021 when a US DoD report published in response to section 1029 of the William M (Mac) Thornberry National Defense Authorization Act for Fiscal Year 2021 found that: ‘The [naval] shipbuilding industry faces a significant challenge in achieving and sustaining required workforce levels, and the industrial base today lacks the resiliency and bench strength to meet required demand.’
The report called for significant action within the industry to develop policies aimed at establishing, accelerating and growing the labour force. These efforts, it stated, were ‘imperative’.
Fast forward three years and the same report is being quoted repeatedly, and the same problems are still found within the industry, leading to significant delays, not only for the USN but also the US Coast Guard and – one has to predict – eventually for the (in)famous Australian submarines built under AUKUS.
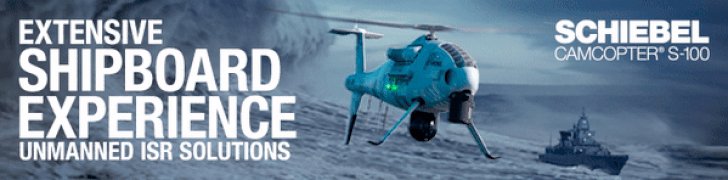
Schiebel – leading the unmanned evolution
A closer look at research carried out on the shortage of skills in manufacturing sheds light on some of the main challenges that need to be addressed.
The general population’s perception of manufacturing jobs is generally quite negative. This is an industry that is seen as featuring mainly low wages and difficult conditions, and is located in areas that have little to offer in terms of lifestyle beyond the day job.
Deloitte and The Manufacturing Institute’s 2022 Manufacturing Perception Study, for instance, found that only 40% of respondents are likely to encourage their child to pursue a career in manufacturing. It also highlighted that few people who are not familiar with the sector think entry-level US manufacturing jobs tend to pay more than other industries (34%) or provide job security (43%).
The sector’s relationship with technological advancements, such as automation and digitalisation, hardly plays in favour of a better perception. For many people, these two words are synonymous with unemployment, with machines and computers edging humans out, so why should they apply for these jobs if they fear being replaced soon?
Other articles in this newsletter:
Throwing new light – could directed energy weapons tip the Red Sea balance?
Power projection or sales pitch? Why the Italian Navy is heading for the Pacific
The reality, however, at least for the foreseeable future, is that these changes in the manufacturing industry come with a demand shift toward more skilled labour. Workers with specialised knowledge in automation, engineering, robotics, programming and related technical fields are indispensable.
But this feeds into another issue plaguing the sector: training. It is hard to gain a comprehensive overview of what the shipbuilding industry has implemented to improve and increase training over the past few years. However, seeing that yards are still struggling to find the required skilled workforce, it would seem that it is insufficient.
A major factor is that the current manufacturing workforce is ageing and there is little to no interest in these types of jobs from younger generations.
Newer generations – Millennials and Gen Z – approach their job search in a very different manner. They value work-life balance, which the locations in which manufacturing jobs are available seldom offer – at least not to the standards they now demand.
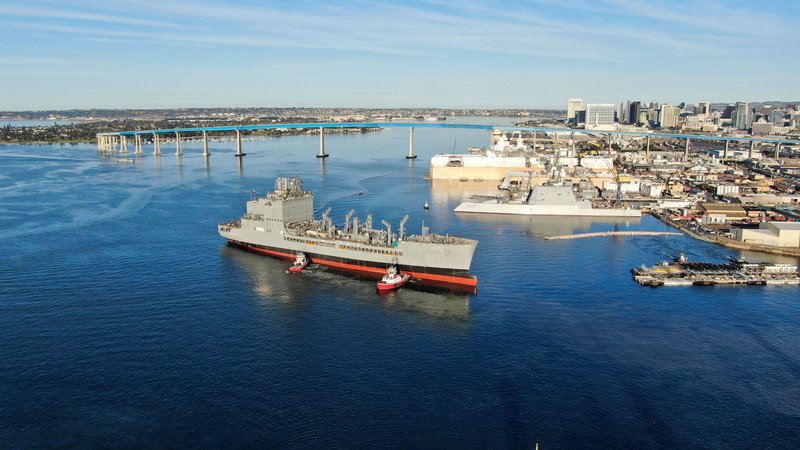
Above: The location of major US shipyards can be seen as a factor in the difficulties of finding a suitably skilled workforce. (Photo: General Dynamics NASSCO)
They value a job that gives them a purpose in life and/or that has meaning. And with the rather negative perception of manufacturing industry and, let’s face it, the defence sector, it is hard to attract new talents. (Especially if they are unaware that these areas of work are evolving and could, potentially, meet their needs.)
But all is not lost. For instance, in FY2023, FMM benefitted from $50 million of funding that was used to attract and retain the workforce. The main efforts focused on distributing bonuses based on ship delivery, developing apprenticeship programmes – which have the potential to reach the younger population more directly and change perceptions – and housing improvements, together with local government.
Ultimately, the workforce is changing. A younger generation, more attuned to its own needs, is now entering the labour market. Manufacturing industry needs to follow these trends, and create its own narrative of what a manufacturing job, such as welder, could be and might bring to the community and – in the case of naval shipbuilding – to the country.
Because, as former Deputy Defense Secretary David Norquist, now president and CEO of the National Defense Industrial Association said during a Congressional hearing: ‘A brittle industrial base is a strategic vulnerability. A resilient industrial base is a deterrent.’
Don't want to miss out on future Decisive Edge content? Make sure you are signed up to our email newsletters.